Dental Innovation Award 2023
Cooperation project "InnoPrintIve" honoured
Over the last 30 years, composite restorations have become established and proven successful in the posterior region. While today it is routine to produce individual or a few fillings directly in the mouth, it is much more strenuous for the patient and also the dentist if numerous teeth destroyed by wear have to be reconstructed. Modeling the anatomical shape and correct height directly in the mouth not only requires almost artistic skills, but also takes a relatively long time. The alternative of having the occlusal surfaces produced in the laboratory is very expensive and not all patients can afford this cost. With the 3D printer, it is possible to print fillings very accurately (deviations of less than 35 µm from the computer-generated ideal shape) outside the mouth. It takes only 15 - 20 minutes to produce these artificial occlusal surfaces in the dental practice. These times have not yet been optimized and could be significantly reduced. The printer is largely based on "open source" or "open hardware" technologies, so that the costs for a printer of this type are relatively low, making the 3D printer attractive not only in industrialized countries with high investment potential, but also in countries with fewer resources.
The special feature of the newly developed 3D printer is that it can print composite materials that are mechanically resilient. This material property is achieved by filling the materials to a high degree with ceramic fillers. The disadvantage of these good properties is the high viscosity of the materials. The viscosity can be reduced by heat in addition mechanical energy helps to dissolve hydrogen bonds. The combination of heat and utilization of thixotropy means that the highly viscous composites can be pressed out through a very thin cannula. The restorations are applied layer by layer and each layer is individually cured during the printing process. The finished objects are then bonded to the teeth using dental bonding technology to restore the original shape.
However, the award-winning version of the 3D printer is not yet suitable for clinical use. Numerous improvements and optimizations still need to be made. The researchers are currently looking for partners with whom further development can be carried out together.
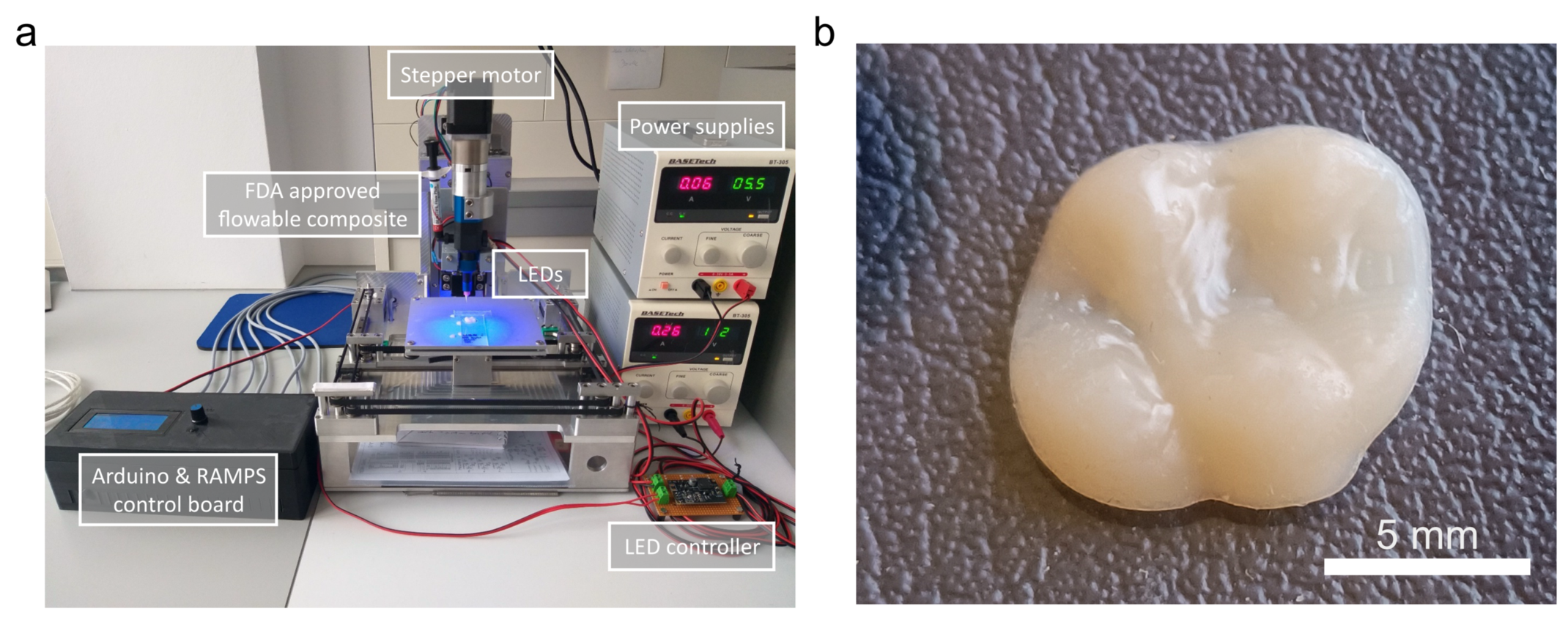
Statement by Prof. Dr. Rösch, Faculty of Computer Science at Augsburg Technical University of Applied Sciences, on the award
"The interdisciplinary cooperation with the group of Prof. Dr. Kunzelmann was established in 2007 and has yielded numerous Bachelor's and Master's Theses, conference contributions and publications in scientific journals. From my point of view, the award-winning printer clearly demonstrates the potential of current open source hardware in combination with free software. Thanks to the University of Applied Sciences and the faculty of computer science for supporting our research by granting sabbatical semesters and teaching load reduction."