The future of Cutting
Ultraschallunterstützung für die Zerspanung von Faserverbundkeramiken
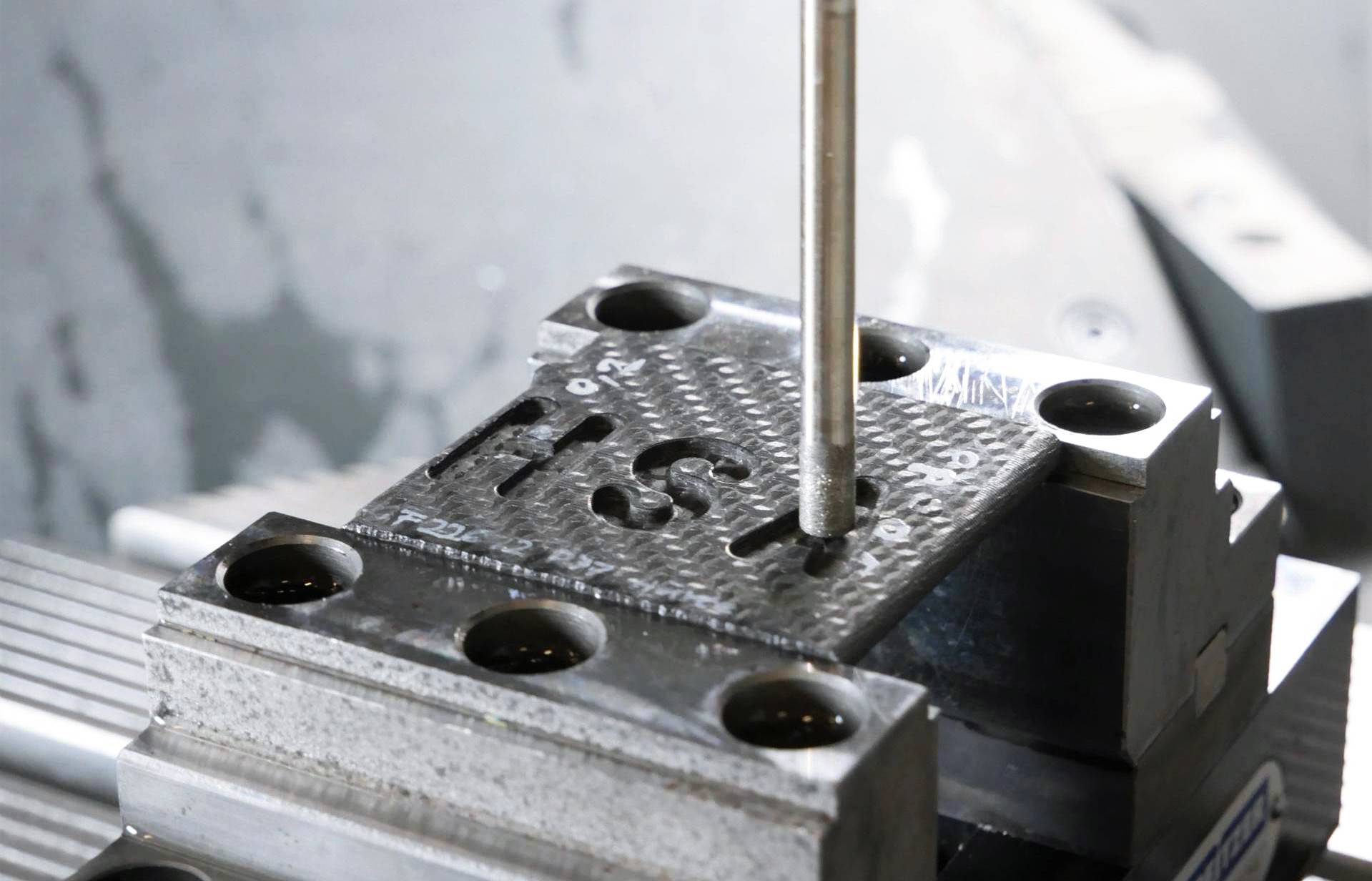
Projektbeschreibung
Im Projekt ULTRACUT der HSA_comp wird ein innovatives, ultraschallgestütztes Hybridverfahren bei der Zerspanung von Faserverbundkeramiken untersucht. Der Forschungsschwerpunkt liegt auf der Prozess- und Werkzeugauslegung zur Entwicklung eines optimierten Prozesskennfelds für eine stressreduzierende und ressourcenschonende Bearbeitung im Vergleich zu konventionellen Verfahren ohne Bearbeitungsqualitätsverlust. Dabei werden die prozessentlastenden Effekte dieser Technologie auf das Materialabtragverhalten sowie auf Qualitäts- bzw. Prozesskenngrößen analysiert.
Keramische Verbundwerkstoffe (Ceramic Matrix Composites, kurz CMC) sind leichte und hochtemperaturstabile Werkstoffe, die in den vergangenen zehn Jahren eine immer größere Rolle
bei energieeffizienten Hochtemperaturbauteilen einnehmen. Hauptanwendung finden sie besonders in der thermischen und chemischen Industrie sowie im Automotivesektor bei Hochleistungsbremsen. Aufgrund ihres herausragenden thermomechanischen und ‑physikalischen Eigenschaftenprofils bis weit über 2.000 °C liegt ein großes Potenzial im Bereich der Luft- und Raumfahrt zur Ablösung metallischer Werkstoffe in bspw. Antriebssystemen. Der Zerspanungsprozess ist zeitaufwändig und kostspielig und daher für eine zukünftige Serienfertigung momentan nicht geeignet
Obwohl CMC-Bauteile endkonturnah („near net shape“) hergestellt werden, ist eine Endbearbeitung erforderlich, um die engen geometrischen Toleranzen und Anforderungen von Funktionsflächen zu erfüllen. Dabei sind die hohe Materialhärte, die niedrige Wärmeleitfähigkeit und das heterogene Gefüge der CMCs die größten Herausforderungen für Fertigungstechniker.
Ultraschallenergie nicht nur im Dentalbereich
Das Team von Prof. Dr.-Ing. Goller entwickelt bereits seit einigen Jahren ressourcenschonende und effiziente Prozesse zur Bearbeitung von Faserverbundkeramiken. Die Anwendung verschiedener Prozesstechnologien wird mit modernen Bearbeitungsmaschinen erprobt. An diesem Punkt setzt das Projekt ULTRACUT an. Im Teilprojekt eines vom Bundesministerium für Bildung und Forschung (BMBF) geförderten Forschungsvorhabens (FHInvest: „CERAMEC“) wird ein innovatives, ultraschallgestütztes Verfahren erforscht.
Auf das große Potenzial der Ultraschalltechnologie wird neben dem Medizinbereich auch in einer ganzen Reihe anderer technischer Anwendungen zurückgegriffen. Insbesondere bei spröd-harten Werkstoffen – wie bspw. Hochleistungskeramiken – wirkt sich ihre Anwendung positiv auf den Herstellungsprozess aus. Durch die Überlagerung der Werkzeugrotation mit einer axialen Oszillation im Hochfrequenzbereich können die Prozesskräfte verringert werden. Dadurch lässt sich bspw. die Oberflächenqualität optimieren [1]. Dieser Einfluss wirkt sich wiederum auch auf den Werkzeugverschleiß aus. Die oszillierende Werkzeugbewegung führt zu einer kontinuierlichen Reinigung bzw. Kühlung der Kontaktzone und damit zu einer verlängerten Werkzeugstandzeit [2].
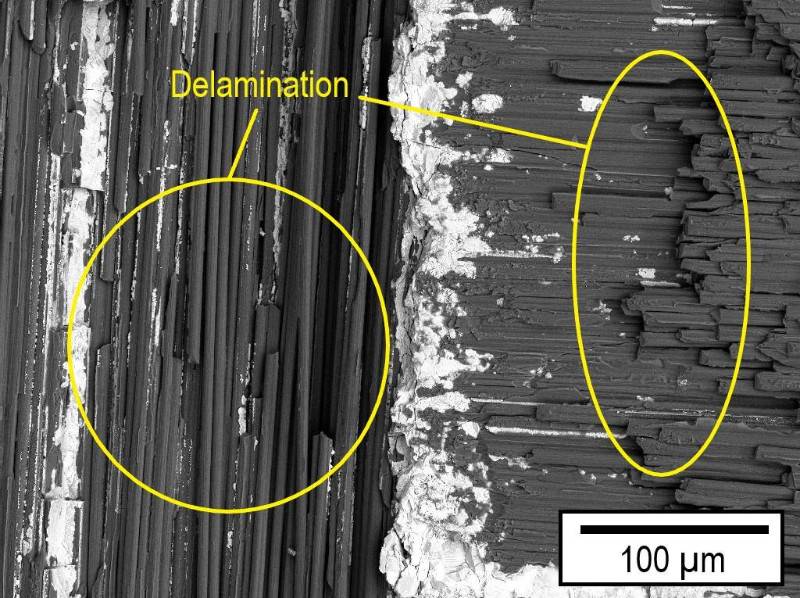
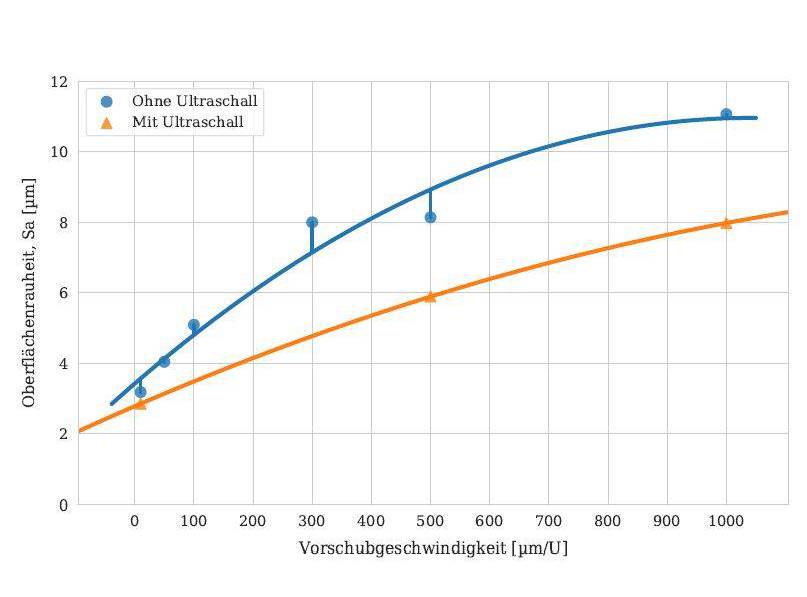
Forschung und Entwicklung
Im Projekt ULTRACUT werden die prozessentlastenden Effekte des Ultrasonic Assisted Machining (UAM ) im Vergleich zum herkömmlichen Schleifen, Fräsen und Bohren von CMCs erforscht. Dazu werden folgende Themen untersucht:
- Charakterisierung und Auslegung von Werkzeugen für die UAM
- Schwingungsanalyse
- Untersuchung des Einflusses auf die Prozesslasten sowie auf die Bearbeitungsqualität (Oberflächenrauheit bzw. ‑topographie, Maß- und Formgenauigkeit, Imperfektionen)
- Abstimmung von Werkzeugen, Ultraschallschwingung und Prozessparametern
- Optimierung der Prozesse
Die Bearbeitungsexperimente werden mit verschiedenen Diamantwerkzeugen an einem Fünf-Achsen-Bearbeitungszentrum mit integriertem Ultraschallschwingungssystem an der Arbeitsspindel durchgeführt. In Abhängigkeit von der Werkzeuggeometrie und ‑masse und des Frequenzbands (15 – 60 kHz) können definierte Schwingungsamplituden bis zu 15 μm vollautomatisch eingestellt werden.
Die Schwingungskenngrößen (Frequenz, Amplitude) werden je nach Werkzeug angepasst und optimiert. Die resultierenden Prozesskräfte am Werkstück werden mittels Dynamometer gemessen und aufgezeichnet. Die Qualität der CMC-Bauteile wird anschließend mittels digitaler Licht- und 3D-Mikroskopie bewertet.
Die bisherigen Ergebnisse (vgl. Bild 3) zeigen beim ultraschallgestützten Fräsen von C / C-SiC mit hohen Vorschüben eine Abnahme der Rauheit um bis zu 30 Prozent gegenüber konventioneller Zerspanung.
Optimierungspotenzial
Die UAM birgt Optimierungspotenzial bei der Entwicklung prozesssicherer und effizienter Bearbeitungsprozesse mit verringertem Werkzeugverschleiß, verbesserter Oberflächengüte und
gesteigerter Abtragleistung. Durch die optimale Auslegung der Prozesskenngrößen und des Werkzeugs will das ULTRACUT-Projektteam das maximale Leistungspotenzial dieses Hybridverfahrens zur Bearbeitung von CMCs für die jeweilige Anwendung ausschöpfen.
[1] O’Toole, L.; Kang, C.; & Fang, F. (2019): Advances in Rotary Ultrasonic-Assisted Machining. In: Nanomanufacturing and Metrology, 1-25.
[2] Liu, Y.; Liu, Z.; Wang, X.; & Huang, T. (2020): Experimental study on tool wear in ultrasonic vibration–assisted milling of C / SiC composites. In: The International Journal of Advanced Manufacturing Technology, 107(1), 425-436.
Projektleitung
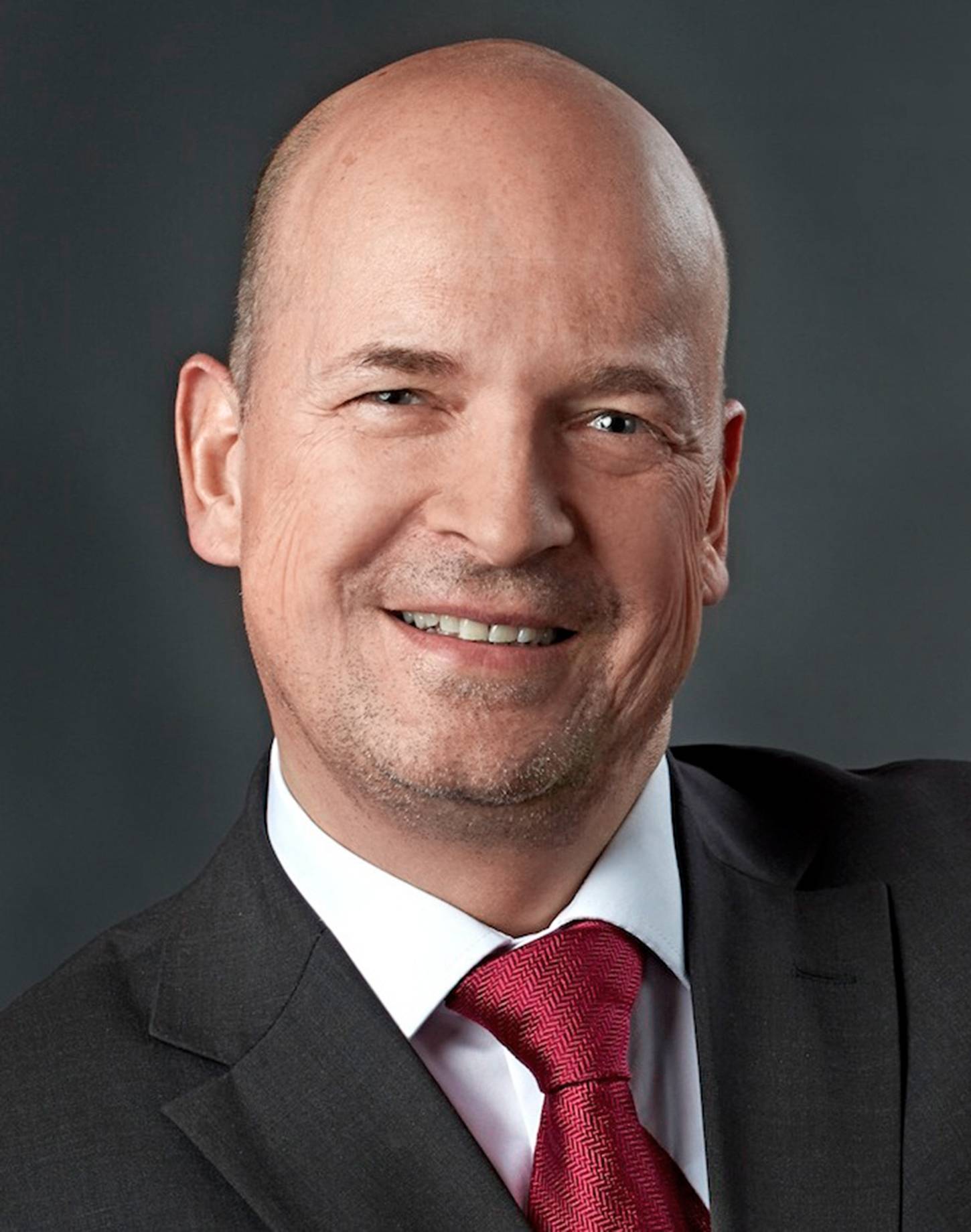
Ansprechpartner | |
Telefon: | +49 821 5586-2068 |
Weitere Beteiligte
Ansprechpartnerin | |
Telefon: | +49 821 5586-2069 |