VIP-Met
Entwicklung eines vollautomatisierten Inlineprüfsystems zur Prozessoptimierung in der Metallverarbeitung
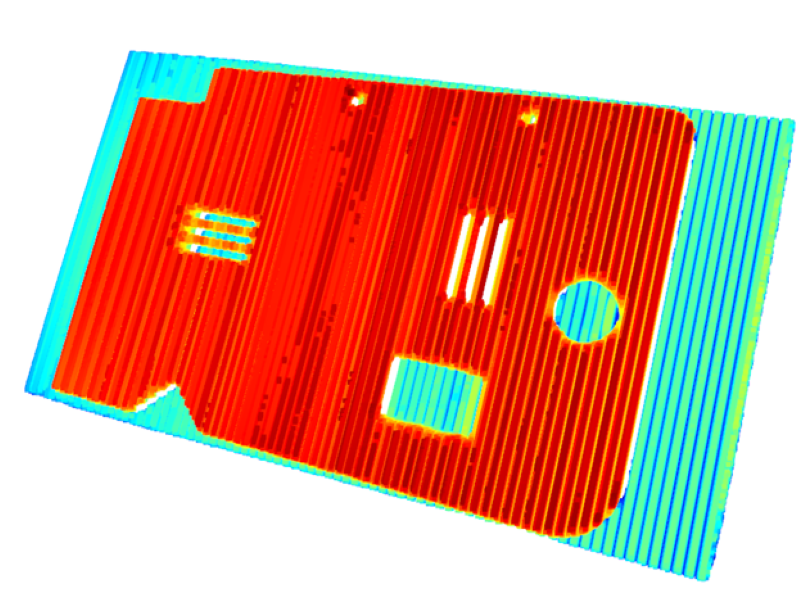
Projektbeschreibung
Ziel des Projekts ist die Entwicklung einer automatisierten Inline-Prüfzelle zur präzisen Vermessung von Werkstücken, die im Verbund mit Schleifmaschinen unterschiedlicher Hersteller betrieben werden kann. Durch den Einsatz kostengünstiger bildgebender Systeme und KI-basierter Algorithmen sollen Werkstückgeometrien hochgenau erfasst und Prozessparameter von Werkzeug- und Schleifmaschinen automatisch nachgeführt werden. Dadurch wird eine gleichbleibend hohe Produktqualität gewährleistet und die Effizienz in der variantenreichen Produktion gesteigert.
Motivation
In der Metall- und Blechbearbeitung, einem zentralen Vorfertigungsprozess für Branchen wie den Automobil- und Flugzeugbau, müssen Werkstücke nach der Fertigung oft nachbearbeitet werden. Aktuell erfolgt die Qualitätskontrolle bei Serien mittlerer und kleiner Stückzahl meist manuell, was zu späten Fehlererkennungen, erhöhtem Ausschuss und inkonsistenter Produktqualität führt. Menschliche Fehler in repetitiven Aufgaben beeinträchtigen zudem die Konsistenz. Um Material und Ressourcen effizienter zu nutzen und Taktzeiten zu reduzieren, benötigen KMUs automatisierte, prozessintegrierte Inspektionssysteme. Diese ermöglichen eine kontinuierliche Datenerfassung für Analyse und Prozessoptimierung und sind essenziell, um in einer wettbewerbsorientierten Industrie und im Zeitalter von Industrie 4.0 zukunftsfähig zu bleiben.
Ziele und Vorgehen
Das Projekt zielt darauf ab, eine automatisierte Prüfzelle zu entwickeln, die Werkstückaußenabmessungen, Ausschnitte und Kantenverrundungsprofile mit hoher Genauigkeit erfasst. Mittels kostengünstiger 2D-Kameras und KI-basierter Algorithmen sollen Messgenauigkeiten im Submillimeterbereich erreicht werden, selbst bei variantenreichen Werkstückgeometrien und ohne manuelle Neuparametrierung. Die Daten mehrerer, teils synchronisierter Kamerasysteme werden fusioniert, um sowohl die Kantenradien als auch die geometrischen Merkmale exakt zu erfassen. Für das Training der KI-Algorithmen werden sowohl synthetische Daten als auch reale Bildaufnahmen eingesetzt, um eine robuste und präzise Analyse unter unterschiedlichen Bedingungen sicherzustellen. Die Bildverarbeitungsalgorithmen sind so optimiert, dass sie den Durchsatz der Produktionslinie nicht beeinträchtigen. Die gewonnenen Messdaten werden zur automatischen Anpassung der Prozessparameter an den vorgelagerten Werkzeug- und Schleifmaschinen genutzt, um durch eine permanente Regelung im geschlossenen Fertigungsprozess ein gleichbleibend hohes Qualitätsniveau sicherzustellen. Standardisierte Datenformate und Schnittstellen ermöglichen zudem die Integration des Systems in bestehende Anlagen und fördern die fortlaufende Verbesserung der Produktgüte durch Datenanalyse und Prozessoptimierung.
Beteiligte Personen
Projektleitung
Telefon: | +49 821 5586-3433 |
Konsortium
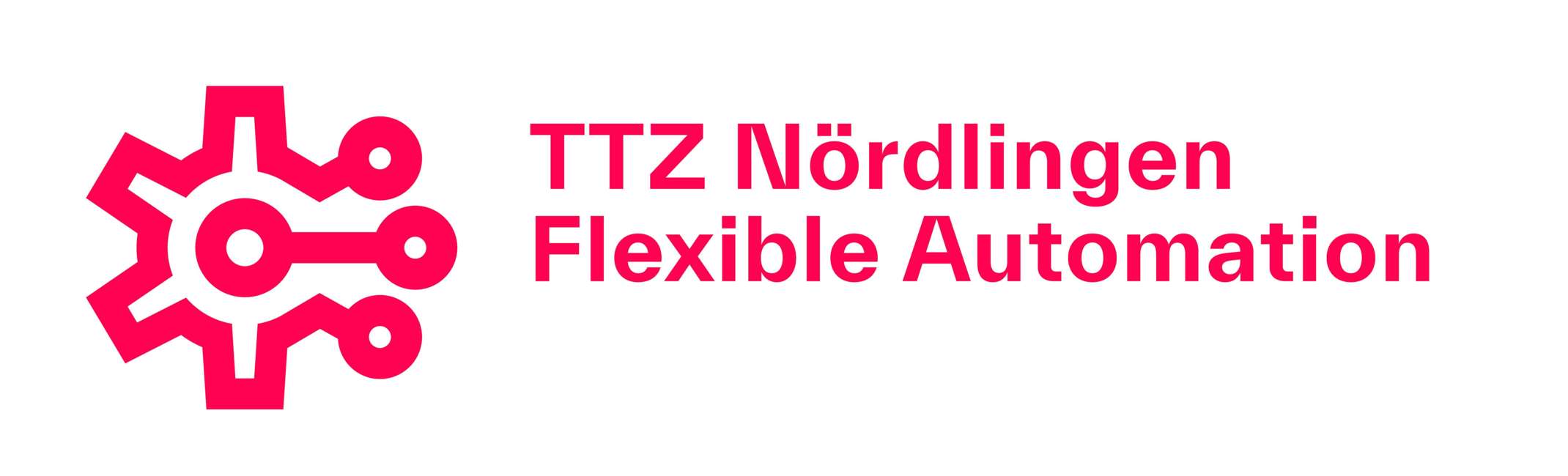
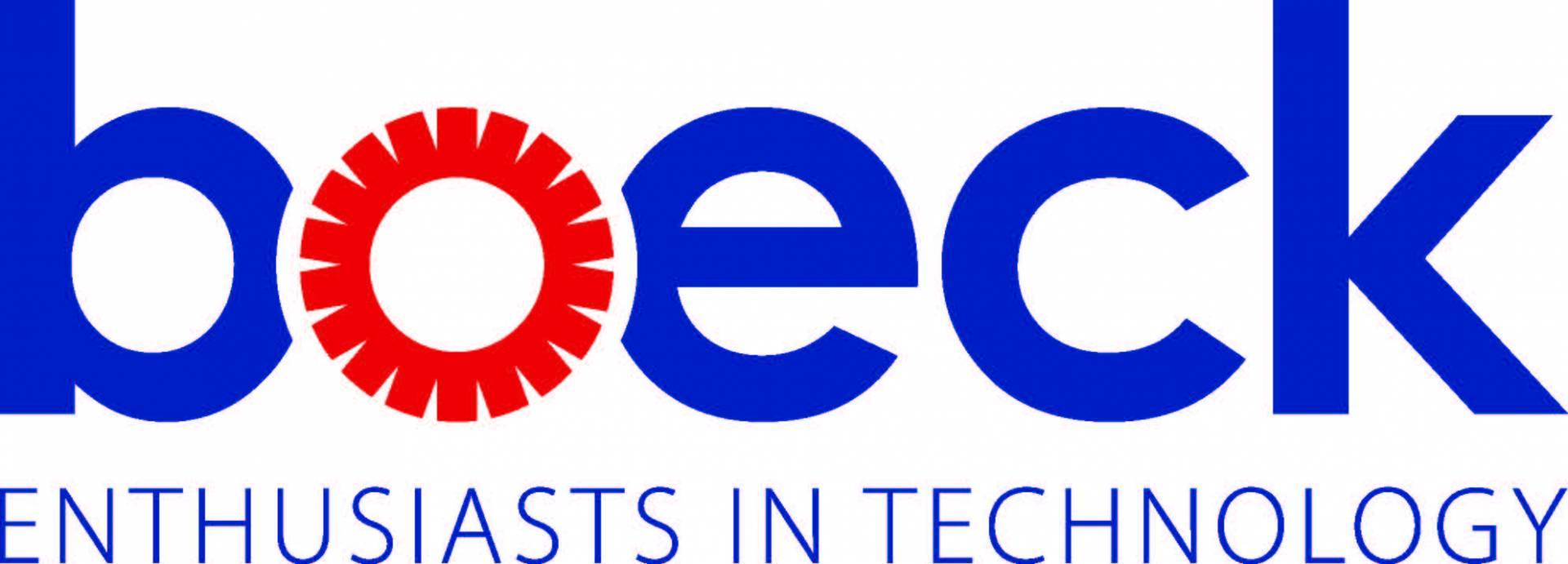
Förderung
Dieses Forschungsprojekt wird durch das zentrales Innovationsprogramm Mittelstand (ZIM) des Bundeministerium für Wirtschaft und Klimaschutz (BMWK) gefördert.
(Förderkennzeichen: 16KN122021)
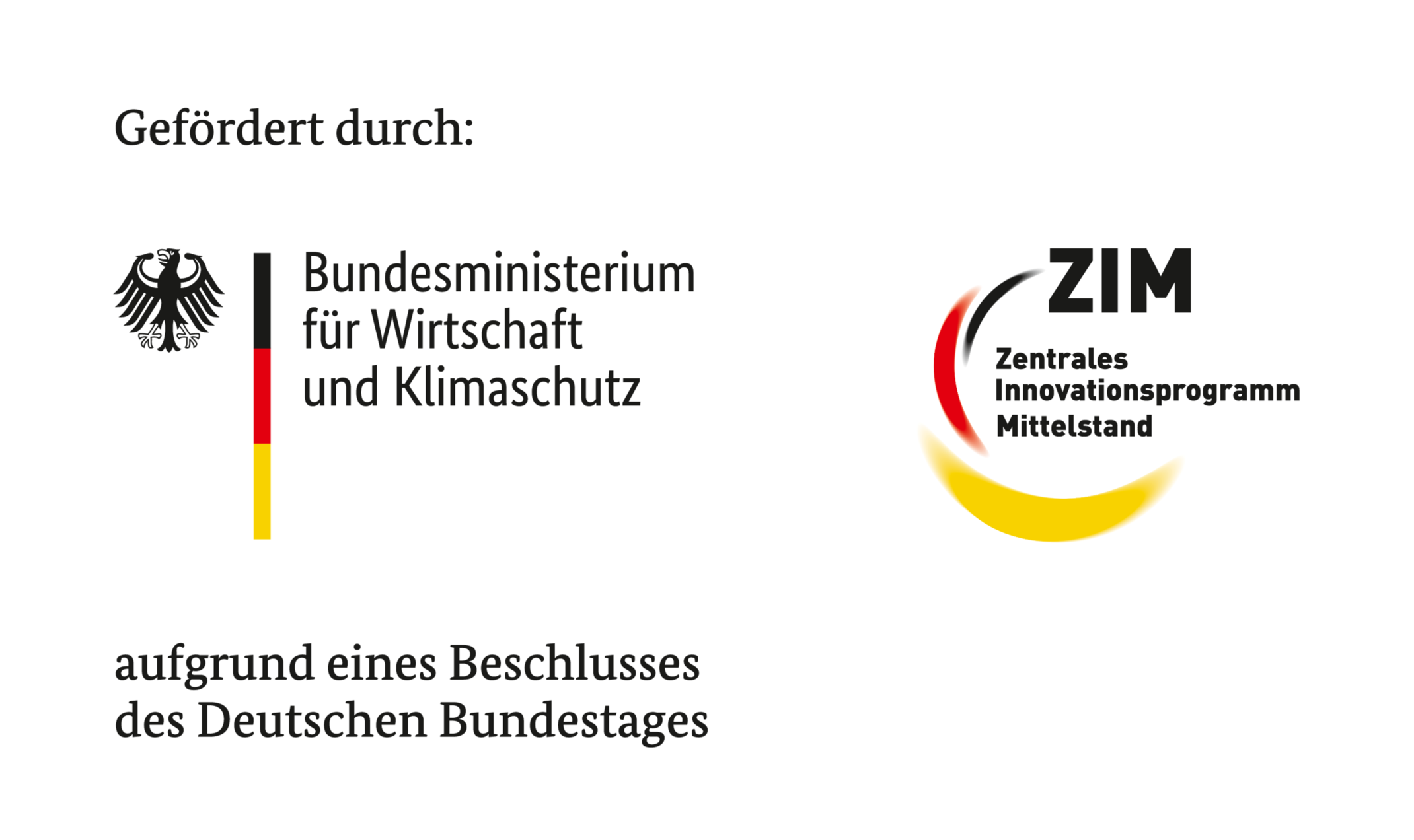